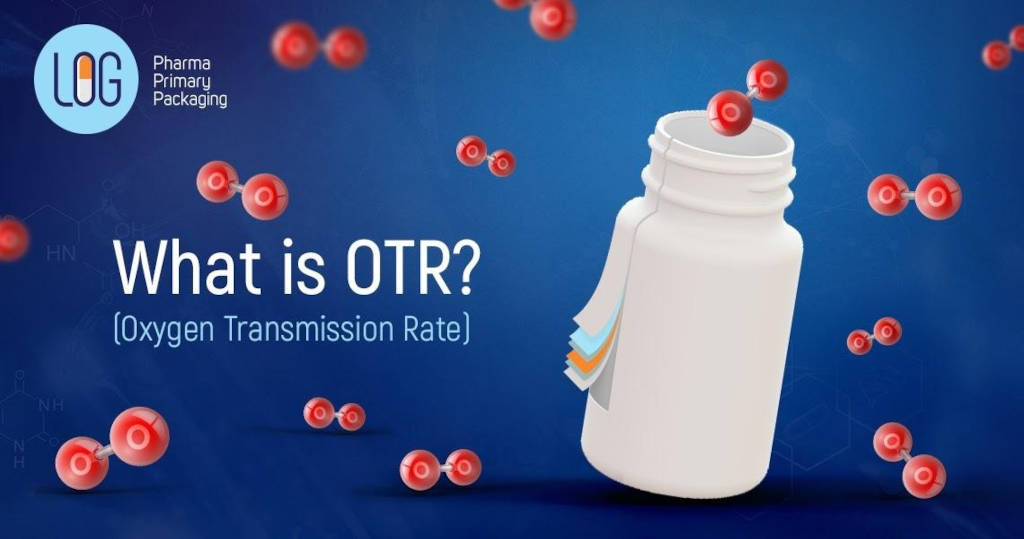
Many of today’s pharmaceutical formulations, to some degree, are sensitive to oxidation. Besides a loss of efficacy and reduction in shelf life, exposure to oxygen can result in product discoloration, toxicity, or other pharmacological properties associated with negative side effects. Within this article, LOG presents insights about OTR testing and its oxygen barrier bottle portfolio.
Oxygen Transmission Rate
- Definition: Oxygen transmission rate (OTR) is the rate at which oxygen molecules traverse through a solid material over a given time period.
- Permeability: All polymers are permeable to gases and vapors to different extents, and oxygen is no different.
- Rate in Packaging: In terms of packaging, OTR is the rate at which oxygen molecules will permeate through the package wall
- Measurements: OTR is measured in cc/bottle per day
When a plastic bottle exhibits a very low oxygen permeation rate it is considered an oxygen barrier bottle. The lower the oxygen permeation rate, the higher the barrier property of the bottle. Key factors with which the OTR of a bottle can be influenced are the characteristics of the raw material, the know-how of using inner barrier layers, and environmental conditions such as temperature and relative humidity.
Testing Container Closure Systems for OTR
The stages for testing packaging for OTR include:
- The package is placed in predetermined environmental conditions.
- The package is purged with pure nitrogen (N2) gas. The N2 forces the existing gas contents (including oxygen) in the package through an outlet tube to a coulometric sensor, which reads the Oxygen content.
- The test output is presented as the volume of oxygen permeated per day per package.
Watch the following real-world case study in which LOG helped its customer to solve peaks of unknown impurity and stabilize their oxygen-sensitive formulation using the right type of passive and active oxygen protection.
Do you have issues stabilizing your oxygen-sensitive formulation?
Testing Container Closure Systems for OTR
LOG performs OTR testing of its barrier packages to enable our customers to predict and calculate the amount of oxygen that will permeate into the packaging in a given time. For this, LOG is following industry standards which provide guidelines on how to perform OTR testing for several applications, including plastic films, sheets, laminates, and rigid plastic packaging.
See how LOG’s oxygen barrier packaging solutions can support you in the development of a safe and stable product that guarantees its utmost efficiency.
LOG’s Barrier Packaging Solutions
LOG’s OxyBlock® and MultiBlock® barrier packaging solutions provide remarkable barrier protection for oxygen-sensitive formulations and are commercially used by leading pharmaceutical manufacturers worldwide.
OxyBlock®
The OxyBlock® bottle provides protection to formulations sensitive to oxygen permeation.
According to laboratory testing, the OxyBlock® barrier bottle performs up to 100x better as an oxygen barrier compared to a standard HDPE bottle.
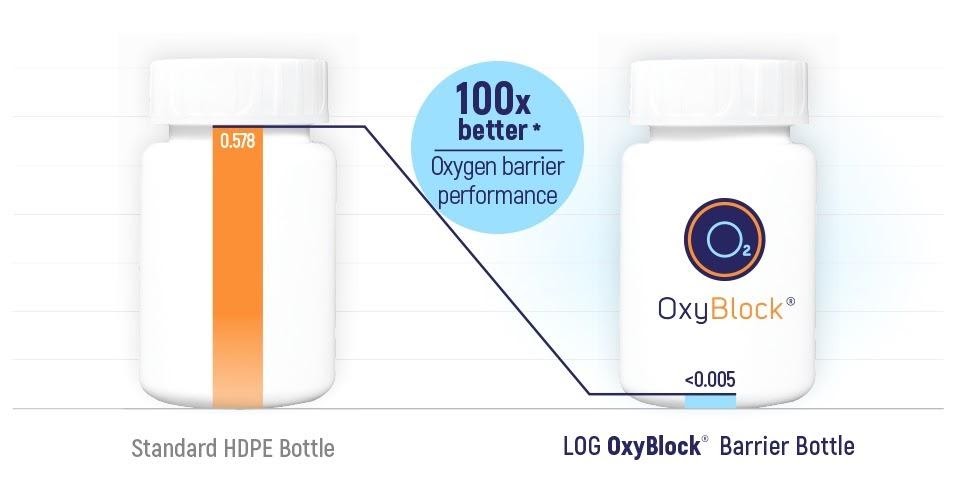
MultiBlock®
The MultiBlock® bottle provides protection for formulations that are sensitive both to oxygen and moisture permeation.
Superior performance tests have shown that the 60ml MultiBlock® bottle has up to 12x better moisture barrier performance and 100x better oxygen barrier performance compared to standard HDPE bottles.
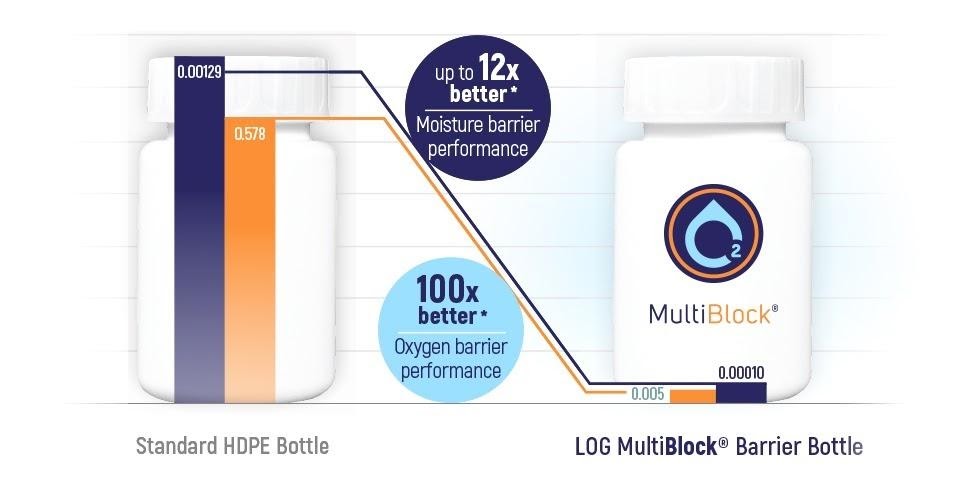
LOG’s barrier bottles are used and endorsed by global pharmaceutical companies and are commercially used in the market for the last 10 years. With LOG’s professional expertise in active and passive barrier packaging, our team of experts would be more than happy to speak with you further and provide you with samples of our innovative barrier packaging solutions for your oxygen-sensitive formulations.
Feel free to contact us for any questions regarding the OTR, including the laboratory test results for our barrier products, which can be provided upon your request. If you produce oxygen-sensitive pharmaceutical formulations, you can be confident in LOG’s knowledge and product portfolio offering you outstanding oxygen barrier packaging solutions for your drug formulation!
About LOG
For the last 50 years, LOG has been serving as a leader in the global pharmaceutical packaging industry, delivering innovative, highly engineered, active, and passive packaging solutions from its manufacturing sites in Israel and Hungary.
LOG adheres to the strictest quality manufacturing standards and is fully committed to compliance with GMP standards for primary packaging. The quality management systems (QMS) of both manufacturing sites are ISO 9001 and ISO 15378 certified.
Stay tuned on new pharma packaging innovations LOG will launch during 2021, signing up for our newsletter and by following us on LinkedIn.
Share This Article with the Stability Community!
June 2, 2025
So, you’ve gone through the process of formulating user requirements, chamber selection and purchase. With the equipment in place; how do we go from this [...]
April 26, 2025
It’s Stability Information Month and time to go a little further than regulations and processes and talk about people, namely the ones who comprise the [...]
March 30, 2025
In the pharmaceutical, food, and chemical industries, product stability is paramount. Ensuring that a product maintains its quality, potency, and safety over its intended [...]
Share your questions and experiences
A stabilitarian encounters new situations every day. StabilityHub’s discussion forums give Stabilitarians an opportunity to ask questions and offer solutions to specific scenarios. Join in the conversations with other Stabilitiarians and share your knowledge!
A stabilitarian encounters new situations every day. StabilityHub’s discussion forums give Stabilitarians an opportunity to ask questions and offer solutions to specific scenarios. Join in the conversations with other Stabilitiarians and share your knowledge!